
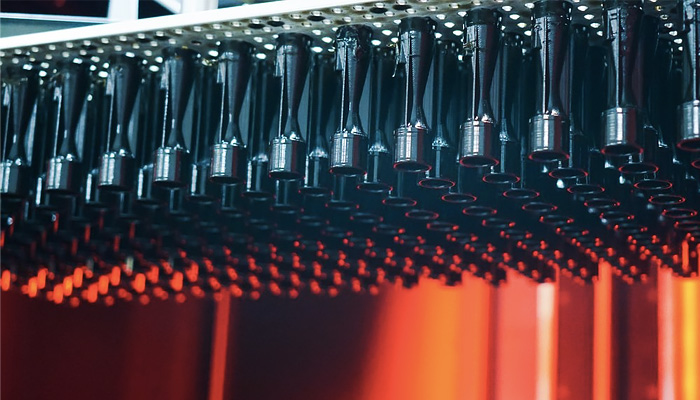
#Mass production 3d printing full#
Whether its customized, 3D printed shoe insoles from companies like Superfeet or more complex offerings like full footwear from Adidas’ partnership with Carbon, buyers are increasingly migrating their loyalty from powerful brands to powerful connections. Consumers are seeking items specifically tailored to them.Īpparel brands are looking to use the digital connection with their customers to deliver personalized products. But now, offering items that are approximately the right size or an acceptable color is not good enough. This compounds the challenge tremendously.įor a long time, customization in the retail world was offered through the same shirt in different colors and sizes, for example. But, in some cases, companies also are expected to produce these small-batch or one-off, customized products in the same amount of time as if they were making them through mass production methods. That in and of itself is a challenging shift. Mass customization manufacturing essentially requires companies to economically produce batches of tens of items when it was previously structured to produce batches of tens of millions through mass production.

What is Mass Customization Manufacturing? All we ask is that you let us serve it your way.”Īlthough the customization of freshly prepared food is a relatively minor task - because the items are assembled by hand anyway - personalization is an even bigger challenge for products commonly made through mass production. “No, sir!” the cashier replies before singing the jingle: “Hold the pickle, hold the lettuce, special orders don’t upset us. In a 1974 commercial, a customer asks if he’ll have to wait long if he customizes a Whopper to remove the pickle and lettuce. With the advantages of 3DPlink print service and multiple advanced thermoplastics can test directly and be an end-use part.Back in the 1970s, American fast-food chain Burger King encouraged consumers to expect mass customization with its “ Have it your way,” slogan. Eventually, the product 3D printed used in final scooter assembly, yield reasonably good results and the customer enjoys the benefits of the 3D print products.ģD printing manufacturing is a good option for small-batch or low-volume production in many aspects of the industry. Comparing with the cost of injection and small quantity, and the surface requirements ask for alcohol resistance in case the paint peeled off while cleaning the surface. 3D printing helped to eliminate costs, as it avoids the need for tool production, which also cuts lead times.Īnother example for small batch production, one of the popular scooter manufacture reach 3DPlink for 300 pieces small batch production for their scooter rear wheel mudguard. In consideration of the time and cost of injection, as well as stock management, they take advantage of 3D printing for their product manufacturing in small batch production. The company took some prototypes for the properties test in their application, after a period of test time, PC-ISO is fully qualified with the product requirements, and it is easy to make EtO sterilization process to help reduce the level of the infectious agents.
#Mass production 3d printing iso#
PC-ISO(polycarbonate ISO), an industrial thermoplastic, is bio-compatible with ISO 10993 and UPS class VI and can be gamma or EtO sterilized. The company found 3DPlink, according to the requirements, 3DPlink came up with the solution of PC-ISO thermoplastic, which is the best option for this product. One of the leading medical equipment companies, l ooking for a bio-compatible plastic for their product, and qualified with any medical class would be better. Engineers not only use this process for prototypes, but they are also using 3D printing for actual manufacturing. But now, it is used for actual manufacturing.
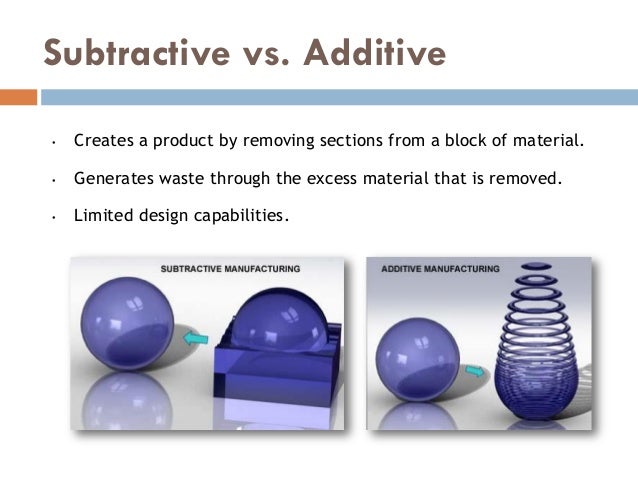
When considering a target quantity of less than 500 – 1000 units, the cost associated with an injection mold tool can become an obstacle.ģD printing additive manufacturing-was originally designed for rapid prototyping. In the past, companies that wanted to produce a plastic product firstly had to create tooling or molds before producing a single end-use product.
